Development of Material Recovery Facility
- Home
- Development of Material Recovery Facility
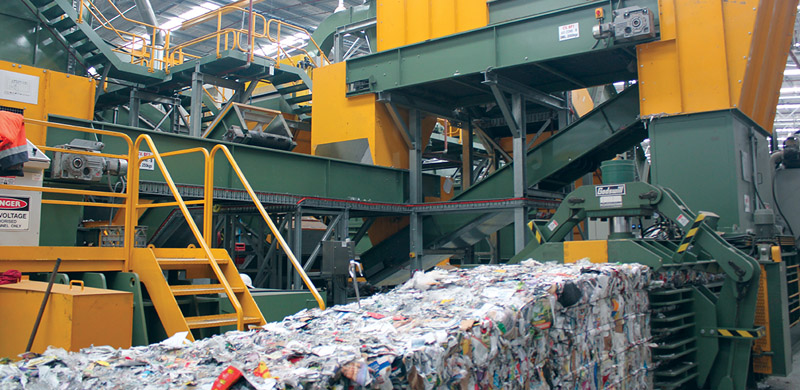
Development Of Material Recovery Facility
A Material Recovery Facility (MRF) is a building to receive, sort, process and store recyclable materials to be shipped and marketed to end-users. A materials recovery facility accepts materials, whether source separated or mixed, and separates, processes and stores them for later use as raw materials for remanufacturing and reprocessing.
The main function of the MRF is to maximize the quantity of recyclables processed, while producing materials that will generate the highest possible revenues in the market. MRFs can also function to process wastes into a feedstock for biological conversion or into a fuel source for the production of energy.
The Materials Recovery Facility (MRF) uses state-of-the-art systems and equipment to recover recyclables from the yellow-topped bin.
Plastic bottles and containers, glass, paper, cardboard, aluminium and steel products are separated and baled at the MRF.
The features of this process are:
1. Commingled Recyclables
Starting in the home, residents place all recyclable material in the yellow-topped bin. These materials are known as ‘commingled recyclables’ and are collected by the Resource Recovery Group’s member councils for delivery to the MRF for processing. At the MRF, trucks unload the commingled recyclables onto the tipping floor. A loader then scoops up the commingled recyclables and places them on a large, slow-moving conveyor belt, which distributes the material for inspection and separation.
2. Quality Control
At a number of points in the process, Resource Recovery Group staff examine the commingled recyclables to remove non recyclable material. Maintaining the quality of the final product is vital to the success of the MRF.
3. Paper Sort and Separation
Through the combined work of automated machines and staff, all paper products are removed from the commingled recyclables. The paper is then further sorted into newspaper, cardboard and ordinary paper. The sorted paper is stored in large bunkers prior to being sent to the baler.
4. Plastics, Metal and Glass Sorting
One of the final steps is for the plastics, metal and glass to be separated, using high-tech optical sorters; the first of their kind in Western Australia. The electronic computer controlled eyes, scan a fast moving conveyor belt looking for type 2 plastics (white opaque plastic used in milk and juice bottles), type 1 plastics (clear cool drink bottles) and all other mixed plastics.
Other machines are used to create electronic fields which repel aluminium and steel containers. Glass is crushed and primed for local use.
5. Balers
Once sorted and separated from the commingled recyclables, the paper, newspaper, cardboard, steel, aluminium and a variety of plastics are transported along conveyor belts to be baled. These baled recycled materials are then used locally, interstate and overseas to make new products; consequently saving energy, resources and greenhouse gases. Glass recovered through the MRF is crushed and used in road base within WA.
Book An Appointment
Let’s Work Together To End Waste.
Send us a request and we’ll get back to you as soon as possible.